Behind the Scenes @ MSU: keeping the water flowing
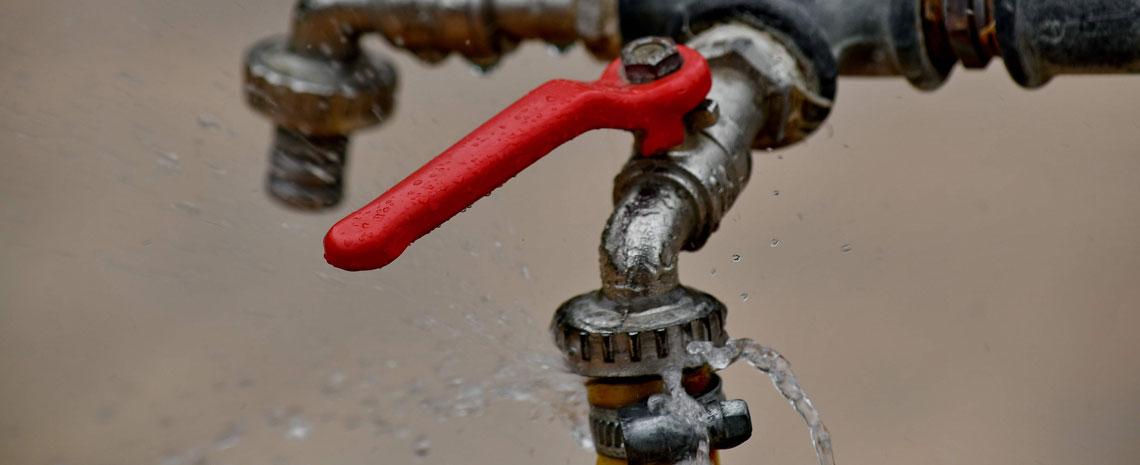
Danielle Fowler
October 20, 2022
This piece is part of a series which highlights the “everyday” work IPF does to support MSU’s teaching, learning and research missions.
Not only does IPF provide electricity and heat to campus, we’re also responsible for providing water services. With almost 50,000 students and more than 12,000 faculty and support staff, that can be a tall order.
That’s why IPF has its own Plumbing Services department.
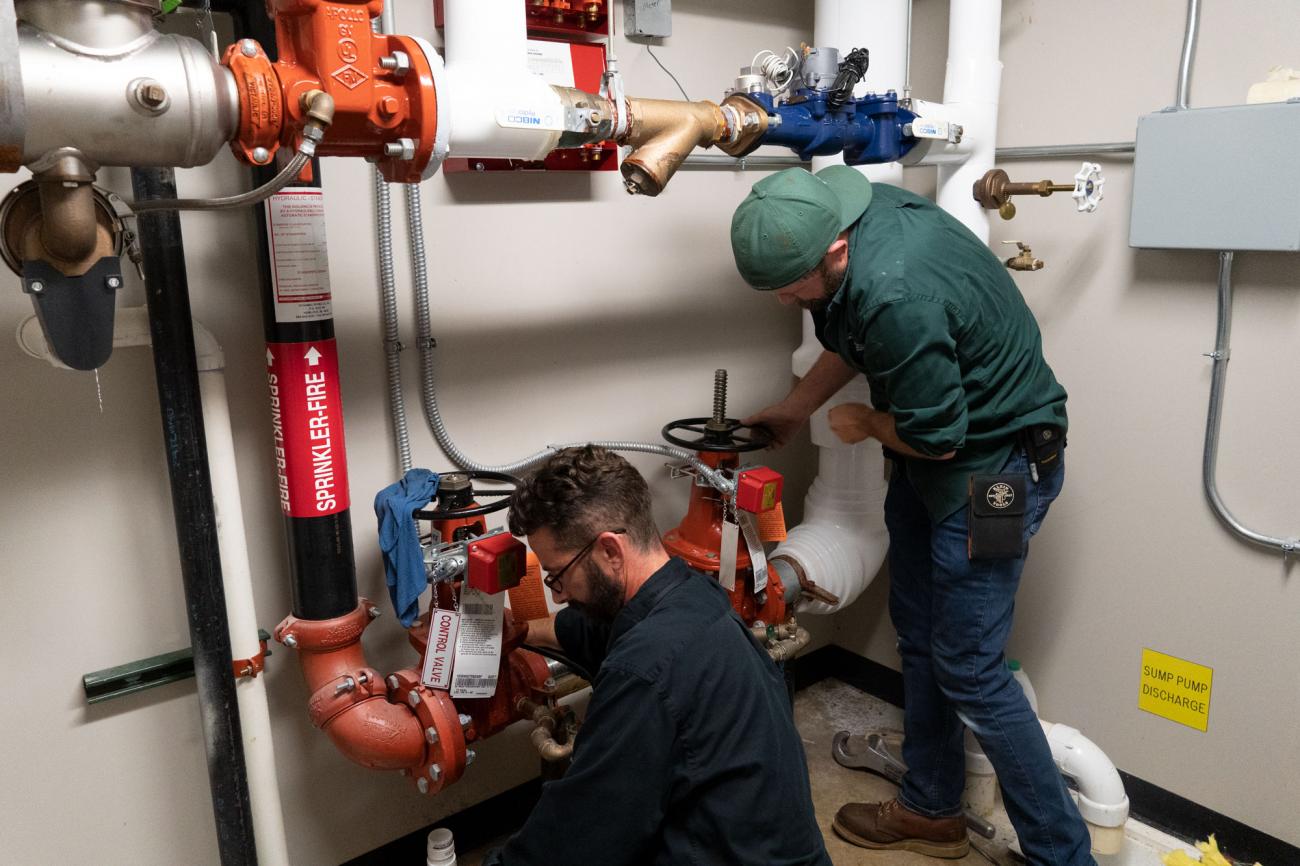
IPF plumbers handle a wide variety of tasks, but on this fall morning plumbers Brian Connolly and Aaron Cyrus are working in University Village to repair a backflow prevention valve.
Backflow prevention valves keep the water we drink clean and safe by preventing contaminated water from flowing backwards into the building, rather than out to be treated.
“I’ve been doing this about five years with MSU and I average about 130 backflow jobs per month,” Connolly says. “We have almost 1,600 backflows on campus and it’s a matter of safety that we keep them all in good condition.”
This particular backflow valve at University Village prevents water from the fire suppression system from mixing with the potable water for the building. Water fills the fire suppression system and stays there in case of an emergency, which means it can become stagnant.
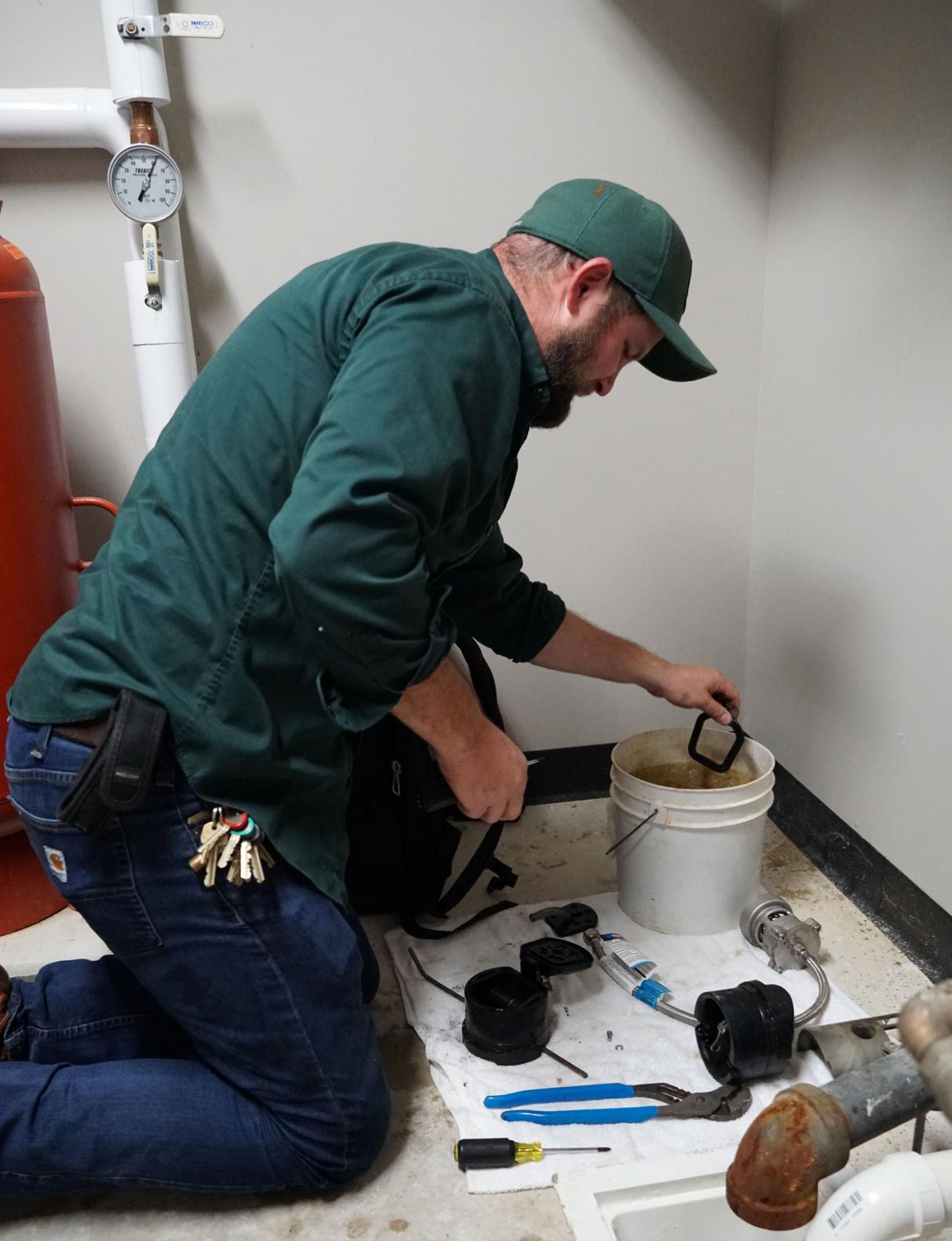
As Cyrus sets up a clean working area with a towel, bucket of water and his tools, he talks about the experience of being a plumber at MSU.
“I used to do commercial construction and installed and built all of these systems,” says Cyrus, “but it’s a very different beast to maintain and repair them. You’re doing a lot of detective work.”
IPF plumbers must also negotiate doing repairs like these while keeping the time that campus customers are without water to a minimum. This calls for a robust schedule of maintenance checks to catch problems before they occur, and going into every job with a plan, especially now that supply chains can be backed up for weeks, if not months.
“We like to look at ourselves as quiet ninjas,” says Connolly. “If you don’t know we’re there, we’re doing our job right.”
Catch our previous feature, Behind the Scenes @ MSU: classroom tech carts.